What Causes Emulsion Paint To Crack
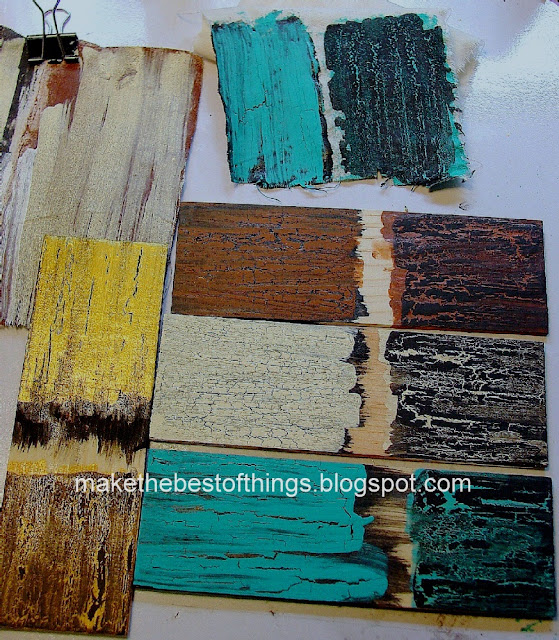
The root of all interior peeling paint is poor adhesion to the previous surface. Here are the ten most common causes of poor adhesion. Stucco: Should You or Should You Not Paint It? Stucco: Should You or Should You Not Paint It? Buy great products from our Interior Wall & Ceiling Paint Category online at Wickes.co.uk. We supply trade quality DIY and home improvement products at great low prices.
Bituminous Surface Treatments . BSTs can provide all of the following: A waterproof layer to protect the underlying pavement. Increased skid resistance. A filler for existing cracks or raveled surfaces. An anti- glare surface during wet weather and an increased reflective surface for night driving. Historically, BSTs have been in use since the 1. BSTs are increasingly in use as a preventative maintenance procedure on flexible pavements of good structure.
Get your weekly DIY fix with our customized newsletter. You've been added to our list. Good stuff is on its way! We have researched and identified the Best Paint (House). Read our reviews to find the Best Paint (House) and compare photos, specs and user reviews.
What Causes Emulsion Paint To Crack Into Pieces
Purpose. A BST offers preventive maintenance from the effects of sun and water, both of which may deteriorate the pavement structure. BSTs create a new wearing course, as well as a waterproof covering for the existing pavement. A BST makes it more difficult for water to enter the base material, and preventing freeze thaw damage for those locations with below freezing temperatures. BSTs also increase the surface friction of the pavement, due to the addition of the cover aggregate. This combats the effects of raveling, which can make the pavement slippery and stopping difficult. A BST gives good, gripping texture to the pavement surface. BSTs should be applied to a distress- free to moderately distressed pavement surface.
A two to four year service life is common, while five year service lives are achievable. Materials. BSTs are created using two main materials: asphalt and a cover aggregate. Asphalt. Asphalt (as asphalt binder, cutback asphalt or asphalt emulsion) and aggregate (uniformly graded). The asphalt is typically an emulsion. Care must be taken with the weather on the day of construction – ideally, a warm day with low humidity is preferred.
BSTs should never be constructed on rainy days or when rain is predicted. Rain can dilute the asphalt binder if it has not yet cured, bringing the binder to the top of the cover aggregate; after the water evaporates, tires can pick up the loose aggregate or track binder across the surface. Cutback Asphalt. While cutback asphalt is historically an option for BSTs, the solvent used (usually gasoline or kerosene) is expensive and potentially dangerous.
A cutback is asphalt dissolved in a solvent, allowing the asphalt to be pumped and sprayed without heating it to high temperatures. The solvent evaporates into the surrounding air, leaving the asphalt binder. Once the solvent has completely evaporated, the cutback has cured. Fast setting time cutbacks use gasoline, while kerosene is used for longer curing times.

- Contractors. Paint contractors get exceptional interior, exterior and commercial coatings and full, personalized support from our network of 5,000+ independently.
- Comparisons to Other Methods. The Silent Paint Remover. Removing multiple layers of paint from an entire house creates a prepared surface for.
- I find nearly all acrylics and emulsions will crack/craze over caulk with only one coat, but after the second coat this goes. I normally run a brush with thinned.
- ACCELERATOR: Additive to paint to speed the cure of a coating. ACRYLIC: A plastic like material used in the manufacturing of paint to.
Cutback asphalt usage has declined in recent years due to pollution and health concerns. Asphalt Emulsion. Today, asphalt emulsions are more commonly used. An emulsion consists of an oil suspended in water.
In this case, the asphalt cement is the oil component. A surfactant (also called an emulsifying agent) needs to be added in order to make the oil and water mix. Having the asphalt suspended in water allows the placing temperature for a BST to be significantly lower than for a hot mix asphalt. A surfactant offers two benefits – one, it causes asphalt to form tiny droplets that will suspend in water by lowering the surface tension between the asphalt and the water. Two, a surfactant determines the electrical charge of the emulsion. Aggregate will have an electrical charge, usually negative. Since opposite charges will attract, it is important to choose an emulsion with the opposite charge, which will enhance the binding of the asphalt to the aggregate.
Cationic (having a positive charge) emulsions are typically used. Figure 1. Close- up of asphalt emulsion being sprayed onto a prepared surface. The spray bar allows for consistent coverage of one lane- width at a time. Figure 2. The emulsion spray bar in action.
Note the distinctive brown color before the emulsion “breaks.”Figure 3. The emulsion color turns to black after it is said to have “broken.”Figure 4.
The aggregate should be added to the emulsion before the emulsion breaks. Note that in this photo, the aggregate was added too late, which is poor procedure. The next largest (by volume) ingredient in an asphalt emulsion is the water. Water forms approximately one- third of the volume of the emulsion. Asphalt particles will, with the help of the emulsifying agent, suspend in the water.
It is important to note that if the emulsion breaks (when the asphalt and water separate from one another) the emulsion will change from brown to black. The aggregate must be applied and rolled before the emulsion breaks. When the emulsion breaks, the water evaporates, and the asphalt remains on the roadway. The asphalt cement is the primary ingredient in a BST. This asphalt is much like the asphalt used in hot mix paving.
Sometimes, a latex or polymer modified asphalt may be used to improve early chip retention or BST durability. Aggregate. Aggregates typically used include natural gravel or crushed stone.
These must be clean and dust free, hard, and uniform. Why We Use Serial Cable To Connect Two Routers Wireless there. This is to provide a durable surface for traffic. It is common to limit the percent of material passing the No. BSTs. Figure 5. The aggregate truck putting down 2. SY application rate of . Receiving hopper of the chip spreader as the truck dumps.
Figure 7. Individual chip gates—this arrangement allows for variable chip application rates. Figure 8. Close- up of chip distribution gates. Figure 9. Application of “choke” stone.
Figure 1. 0. Rolling helps set the stone in the emulsion. Aggregate used in construction of a BST should be placed only one layer thick.
The exceptions to this is when adding chokestone or a second BST layer (a two layer BST is often referred to as a “double shot” treatment). Placing too much aggregate will cause aggregate pickup, whereby the well placed stones are dislodged, and may cause automobile windshield damage. A small amount of excess aggregate, more than 5% but less than 1. This will reduce tire scuffing in the freshly laid BST. Aggregate Shape. Aggregate shape can be described as either flat or cubical. It can also be either round or angular.
These qualities will effect the seal coat in different ways. If an aggregate is flat, the BST will lose chips excessively in the non- wheelpath section of the road bed, or it may bleed in the wheelpath. This is due to the pressure from automobile tires causing the flat chips to settle into the asphalt on their flattest side. The BST then becomes thinner where the tires pass over.
Aggregate with a Flakiness Index of 2. Flakiness is not an issue in low volume applications, as many tire passes are needed in one area to cause this phenomenon. However, for most applications, cubical aggregate is preferred due to its stability. Round aggregate is likely to roll and become displaced by traffic. Angular aggregates lock to one another. Areas with frequent snow plowing must take extra care in order to make sure a BST with a round aggregate will embed properly as the snow plow may shave off the taller pieces of stone.
On high volume roads, a double chip seal may be the better option. This is when a BST is placed atop another one. The aggregate on the bottom layer should be about twice as large as the one on the top. The smaller stones on top will be less likely to cause windshield damage and the surface is typically smoother than a single seal coat. Aggregate Size. Aggregate gradation and size are important to the success of a BST.
Gradation describes the distribution of large and small stones within the aggregate mix. For a BST, the two options are one- size aggregate or graded aggregate. One- size aggregate is an aggregate mix that comprises roughly equal sized stones. If all the aggregate is approximately the same size, there are good void spaces for the asphalt to fill and adhere the stones to the pavement structure. Other benefits of one- size aggregate include good friction between the surface and vehicle tires due to maximizing tire- aggregate contact area, good drainage between stones, and simplicity in determining whether the amount of aggregate is sufficient.
Graded aggregate simply means that the aggregate has some distribution in size.
Interior Wall & Ceiling Paint - Paint - Decorating & Interiorsnever miss a deal. Sign up for weekly offers.